Understanding the Tevo Tarantula Extruder
The Tevo Tarantula is a popular, affordable 3D printer, well-regarded in the maker community. One of the key components influencing its performance is the extruder, the mechanism responsible for feeding filament into the hot end. The extruder’s design significantly impacts print quality, speed, and the types of filaments that can be used. Understanding the extruder is crucial for anyone looking to improve their printing results, whether by optimizing the existing setup or considering upgrades. The choice between the standard and the Titan extruder is a fundamental decision for Tevo Tarantula owners seeking to elevate their 3D printing capabilities. This article explores the key differences, benefits, and considerations to help you decide which is the best choice for your needs.
The Standard Extruder on Tevo Tarantula
The standard extruder that comes with the Tevo Tarantula is a functional, if somewhat basic, system. It’s designed to get you printing quickly, but it has limitations that can affect print quality and the range of filaments you can use. This extruder typically employs a direct-drive setup, where the extruder motor is mounted directly above the hot end. This design has its pros and cons, which we’ll explore in detail. The standard extruder serves its purpose well for beginners, providing a straightforward and relatively simple setup. However, as users become more experienced and seek higher print quality and greater material flexibility, they often look for improvements. The standard extruder’s performance is often a starting point from which users assess the need for upgrades.
Components of the Standard Extruder
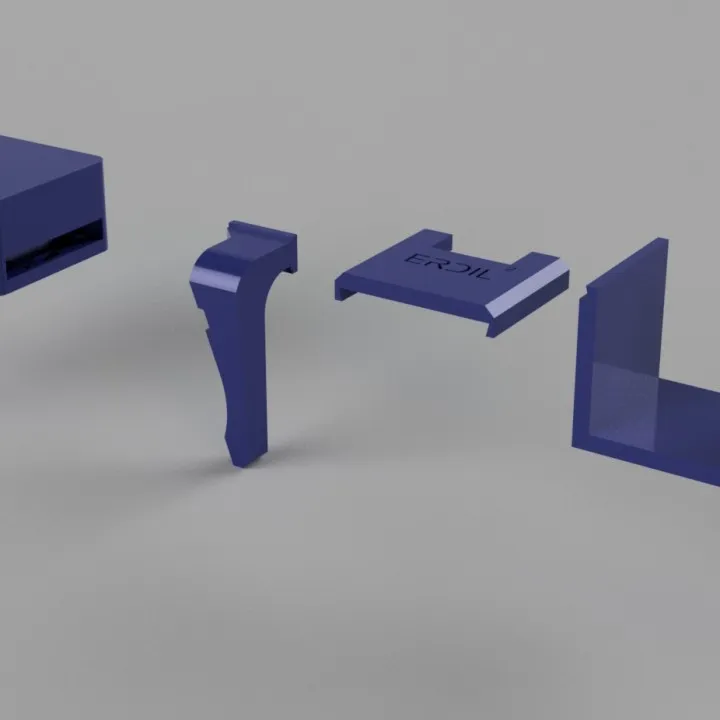
The standard extruder typically includes a stepper motor, a drive gear, an idler bearing, and the extruder housing. The stepper motor provides the torque to push the filament. The drive gear, often a toothed wheel, grips the filament and feeds it towards the hot end. An idler bearing applies pressure to the filament, ensuring it is firmly pressed against the drive gear. The extruder housing holds all these components together and provides a mounting point for the hot end. The quality and precision of these components directly impact the extruder’s ability to consistently and accurately feed the filament. Any issues with these parts, such as wear and tear on the drive gear or insufficient pressure from the idler bearing, can lead to printing problems like under-extrusion or inconsistent layer adhesion. Understanding these components is essential for troubleshooting issues and making informed decisions about potential upgrades or replacements.
Pros and Cons of the Standard Extruder
One of the primary advantages of the standard extruder is its simplicity. It is easy to set up, maintain, and troubleshoot. Its direct-drive design offers good control over filament, especially with flexible materials. However, the standard extruder has drawbacks. It can be bulky and add weight to the print head, potentially leading to vibrations and reduced print speeds. The direct-drive setup also limits the printable area, as the weight of the extruder affects how quickly the print head can move. It’s often less efficient with flexible filaments, as the longer filament path can lead to buckling and jams. The standard extruder may also struggle to handle advanced materials that require high temperatures or precise feeding. Therefore, while the standard extruder provides a good starting point, its limitations become apparent as users explore more demanding printing projects.
Introducing the Titan Extruder
The Titan extruder, manufactured by E3D, is a popular upgrade for the Tevo Tarantula, praised for its performance and efficiency. Unlike the standard extruder, the Titan is designed for both direct-drive and Bowden setups, giving users more flexibility. Its compact and lightweight design reduces the weight on the print head, enabling faster print speeds and improved print quality. The Titan extruder is built with high-quality components, including a hardened steel drive gear and an efficient gear ratio. These features contribute to its superior filament control and ability to handle a wide range of materials. Upgrading to a Titan extruder is a significant step for those seeking to optimize their Tevo Tarantula and elevate their 3D printing results. The Titan extruder aims to resolve the limitations of the standard extruder, providing a smoother, more accurate, and more versatile printing experience.
Key Features of the Titan Extruder
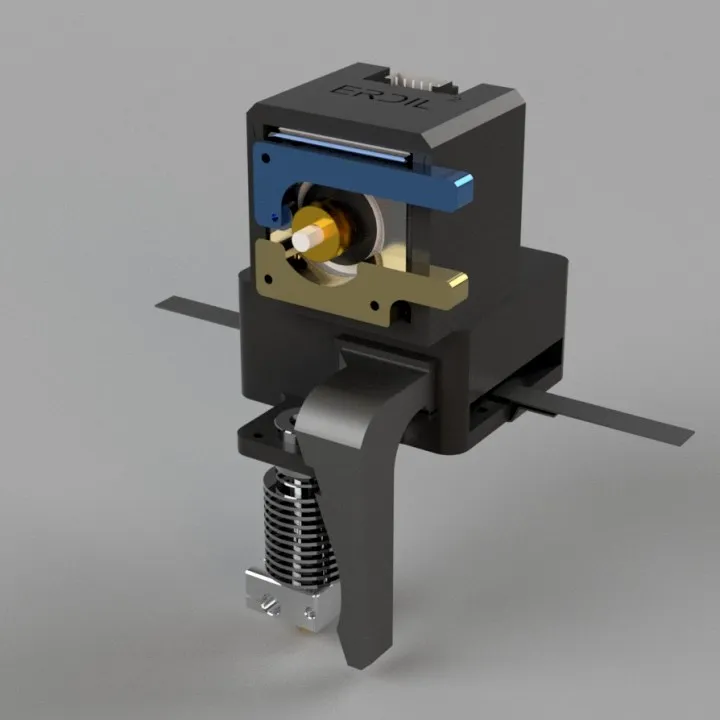
The Titan extruder stands out due to several key features designed to enhance 3D printing performance. It utilizes a geared drive system, typically a 3:1 or 4:1 gear ratio, which amplifies the motor’s torque. This increased torque allows for more precise filament control and the ability to push filament with greater force. The lightweight design minimizes weight on the print head, promoting faster movements and reducing vibrations. The Titan extruder is versatile, compatible with both direct-drive and Bowden setups. Its all-metal design enables it to handle high-temperature filaments, such as nylon and polycarbonate. These key features combine to create a more robust and reliable extruder, improving overall print quality, speed, and material compatibility. The Titan’s thoughtful design and quality construction make it a valuable upgrade for any Tevo Tarantula owner.
Benefits of Upgrading to a Titan Extruder
Upgrading to a Titan extruder offers several significant advantages that enhance the 3D printing experience. These benefits encompass improved print quality, increased speed, and greater versatility with a broader range of filaments. It is a popular choice for those looking to take their Tevo Tarantula to the next level. The Titan extruder addresses many limitations of the standard extruder, providing a more refined and efficient printing system. These advantages are particularly noticeable in the consistency of print results, the ability to handle challenging materials, and the overall reliability of the printing process. The investment in a Titan extruder can lead to more successful prints and a more enjoyable 3D printing journey.
Improved Filament Control
One of the most noticeable improvements with the Titan extruder is the enhanced filament control. Its geared drive system provides greater torque, enabling it to grip and push the filament with more precision. This improved control results in more consistent extrusion, which leads to better print quality. The Titan extruder can handle a wider range of filaments with greater accuracy, including flexible materials. The reduction in filament slippage and the ability to maintain a consistent flow rate contribute to more detailed and accurate prints. This level of control is particularly crucial when printing complex models with intricate details or using materials that are sensitive to extrusion inconsistencies. The Titan extruder offers users a higher level of precision and control over the printing process, resulting in more reliable and visually appealing prints.
Enhanced Printing Speed
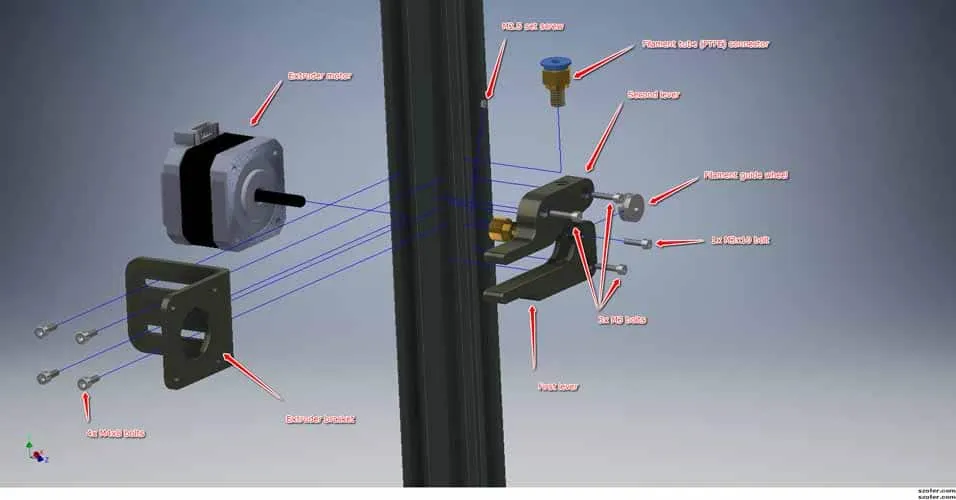
The Titan extruder’s lightweight design and efficient operation enable faster printing speeds. Reduced weight on the print head minimizes vibrations, allowing the printer to move more quickly without sacrificing print quality. The increased torque provided by the geared drive system allows for quicker filament extrusion, which can significantly reduce print times. Many users find that they can increase their printing speeds after upgrading to the Titan extruder without compromising print quality. Faster print speeds mean more productivity, allowing users to complete projects more quickly and efficiently. This is particularly beneficial for those who rely on 3D printing for prototyping, small-scale manufacturing, or creating multiple parts. The ability to print faster while maintaining quality is a major advantage of the Titan extruder.
Increased Filament Compatibility
The Titan extruder expands the range of materials that can be successfully printed on the Tevo Tarantula. Its all-metal design can withstand higher temperatures, enabling it to handle advanced filaments like nylon, polycarbonate, and other high-temperature materials. The enhanced filament control reduces the chances of clogs and extrusion problems, making it more reliable for various filament types. The Titan extruder is particularly well-suited for flexible filaments. Its ability to accurately control the flow of these materials is essential for achieving successful prints. This increased versatility allows users to experiment with a wider array of materials, opening up new possibilities for 3D printing projects. The Titan extruder’s ability to handle a broad spectrum of materials is a significant advantage for users seeking to expand their printing capabilities.
Direct Drive vs Bowden Setup
The Titan extruder’s versatility extends to supporting both direct-drive and Bowden setups. In a direct-drive setup, the extruder motor is mounted directly above the hot end, offering precise filament control and good handling of flexible filaments. However, this setup can add weight to the print head. In a Bowden setup, the extruder motor is mounted on the frame of the printer, and the filament is fed to the hot end through a PTFE tube. This reduces the weight on the print head, which allows for faster print speeds. The choice between direct-drive and Bowden depends on the specific printing needs and the filaments being used. The Titan extruder offers the flexibility to choose the setup that best suits your project requirements. The ability to switch between setups provides greater adaptability and control over the printing process.
Comparing Performance Titan vs Standard
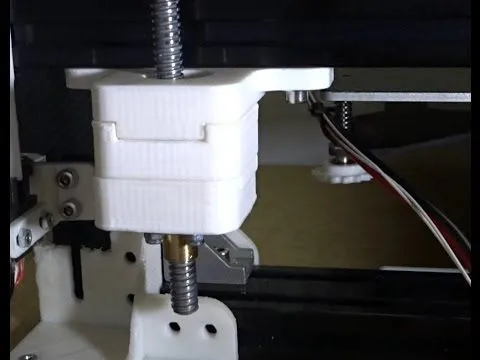
Comparing the performance of the Titan and standard extruders reveals clear differences in print quality, speed, and material compatibility. The Titan typically outperforms the standard extruder in several key areas. The advantages are often most noticeable in more complex prints, with intricate details, or when using challenging materials. Evaluating performance involves assessing print quality, measuring print speeds, and testing filament compatibility. This comparative analysis provides valuable insights into the benefits of upgrading to a Titan extruder. Understanding these differences allows users to make an informed decision based on their printing needs and goals. The performance comparison helps users determine whether the Titan extruder’s advantages align with their specific requirements.
Print Quality Analysis
In terms of print quality, the Titan extruder often produces superior results compared to the standard extruder. The enhanced filament control provided by the geared drive system results in more consistent extrusion, reducing issues such as under-extrusion and inconsistent layer adhesion. The Titan’s lightweight design minimizes vibrations, which can lead to smoother surfaces and more accurate prints. Fine details and complex geometries are typically rendered more accurately with the Titan. Tests frequently show a noticeable improvement in the overall quality of printed parts, especially in challenging areas like overhangs and bridges. The improved print quality translates into more professional-looking and functional prints. The Titan extruder is an excellent upgrade for those looking to achieve higher levels of detail and precision in their 3D prints.
Print Speed Comparison
The Titan extruder generally allows for faster print speeds than the standard extruder. The reduced weight on the print head minimizes inertia, enabling faster movements without sacrificing print quality. The increased torque allows for quicker and more consistent filament extrusion, also contributing to faster print times. While the standard extruder may be suitable for slower, more basic prints, the Titan extruder excels when speed is a priority. Users often find that they can increase print speeds significantly after upgrading. Faster print speeds translate into greater productivity. Testing the print speed reveals measurable differences. The Titan extruder provides a more efficient and productive 3D printing experience.
Filament Compatibility Test
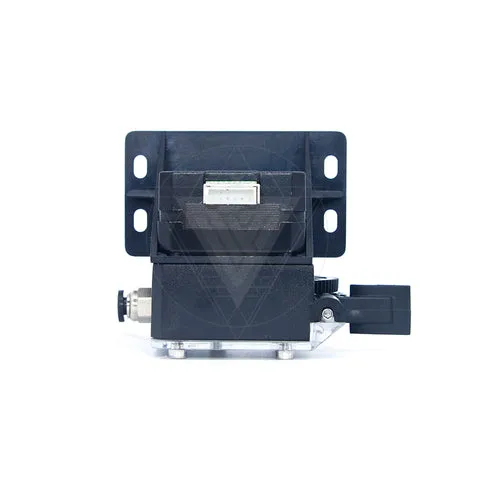
A filament compatibility test highlights the Titan extruder’s versatility. The Titan can handle a wider range of filaments compared to the standard extruder, including materials that require higher temperatures or more precise feeding. The Titan’s all-metal design enables it to print with high-temperature filaments. Testing often involves printing with various filaments, such as PLA, ABS, PETG, nylon, and flexible TPU, and evaluating the results. The Titan extruder demonstrates better performance. It showcases the extruder’s ability to consistently extrude different materials, leading to successful prints. By performing a filament compatibility test, users can verify the Titan’s suitability for their specific printing needs. This is especially beneficial for users who want to experiment with a wider array of materials.
Installation and Setup
The installation and setup process for the Titan extruder is usually straightforward, although it requires some mechanical skill. Understanding the steps involved and having the right tools can ensure a smooth and successful upgrade. Proper installation is essential to avoid printing issues and to ensure the extruder functions correctly. The process involves a few key steps. It’s important to follow the manufacturer’s instructions and to take the time to calibrate the printer after the installation. Proper installation and calibration are necessary to fully realize the benefits of the Titan extruder. The process may require some adjustments to firmware settings. It is important to test and troubleshoot the installation to make sure everything is working as it should.
Installing the Titan Extruder
Installing the Titan extruder typically involves removing the old extruder and mounting the Titan in its place. This often requires disassembling parts of the print head. The specific steps vary depending on whether the user is installing the Titan in a direct-drive or Bowden configuration. Ensure that the mounting hardware is compatible with the Tevo Tarantula’s design. Many guides and videos offer detailed instructions on the installation process. Properly securing the extruder and connecting the necessary wires is vital for correct functionality. Before starting the installation, it’s important to disconnect the printer from the power supply. Then, the user has to carefully remove the old extruder. The Titan extruder should be mounted on the printer’s frame. The user must ensure that all connections are secure. Following the manufacturer’s instructions and taking precautions during the installation are critical to avoid any damage to the printer and ensure that the Titan extruder works correctly.
Calibration and Tuning
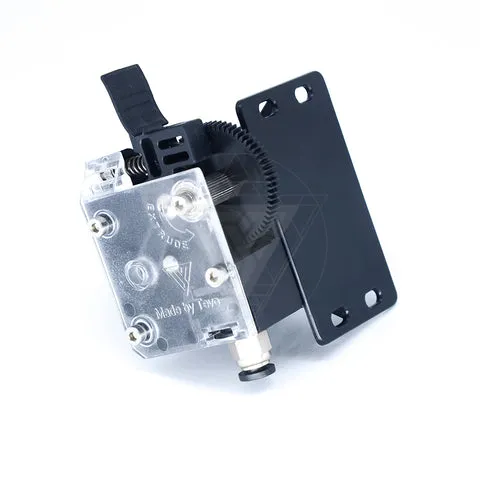
After installing the Titan extruder, it’s essential to calibrate the printer and tune the settings to optimize print performance. Calibration involves adjusting the settings in the printer’s firmware or slicer software. The calibration process ensures that the extruder accurately extrudes the correct amount of filament. Adjusting settings such as the E-steps per millimeter, which determines how much filament is extruded for a given motor step, is often necessary. Other adjustments may include temperature settings and print speed. These settings need to be fine-tuned to match the filament type being used. To calibrate, the user needs to carefully follow the instructions to optimize print performance. Thorough calibration ensures the best possible print quality and results. These steps will vary depending on the user’s printer model and software settings.
Troubleshooting Common Issues
Even with proper installation and calibration, users may encounter some common issues. Common problems include clogs, under-extrusion, and inconsistent layer adhesion. Clogs can occur if the hot end temperature is too low or if the filament is of poor quality. Troubleshooting steps may involve increasing the temperature. Under-extrusion may be caused by incorrect E-step settings or by issues with the filament feeding mechanism. Inconsistent layer adhesion can arise from improper bed leveling, incorrect print speeds, or insufficient cooling. Addressing these issues typically involves troubleshooting the printer settings. Proper calibration and regular maintenance can often resolve many of these problems. The user should be prepared to address possible issues, which helps ensure a smooth and successful 3D printing experience. The user can seek help from online resources, such as forums and troubleshooting guides.
Making the Right Choice for Your Tevo Tarantula
Deciding whether to upgrade from the standard extruder to the Titan is a personal choice. It depends on printing needs, budget, and the level of experience the user has with 3D printing. The standard extruder offers a simple, straightforward experience for beginners. However, the Titan extruder provides significant advantages in terms of print quality, speed, and material compatibility. Consider the types of prints you’ll be doing, the materials you want to use, and the level of performance you require. If you’re seeking higher print quality, faster print speeds, or greater material flexibility, then the Titan extruder is a worthwhile upgrade. Before making a decision, evaluate your specific printing needs. If you primarily print basic models with PLA, the standard extruder might suffice. The user will benefit from the Titan extruder. Researching both options can help you make an informed decision that aligns with your goals.